BEAST KNOWHOW
Was können wir, was die anderen nicht können? Was unterscheidet unsere Komponenten von anderen? Die Antwort liegt in unserer Herkunft. Hinter Beast Components stecken nicht nur Fahrrad-Nerds, sondern vor allem Leichtbau-Experten. Durch unser Knowhow holen wir aus Carbon all das raus, was in ihm steckt.
CARBON SKILLS
Carbon ist unsere Leidenschaft. Häufig fragen wir uns, woher das schlechte Image von Carbon Komponenten für Fahrräder stammt. Wir können es uns nur so erklären – von schlechten Carbon Komponenten. Wir bedauern dieses Image, denn die Eigenschaften von Carbon und dessen Vielfalt sind faszinierend.
Carbon ist ein Faserverbundwerkstoff, der in unzähligen Branchen eingesetzt wird und auch in der Fahrradindustrie boomt. Bei einem Verbundwerkstoff handelt es sich um zwei Werkstoffe, die kombiniert werden, um so die positiven Eigenschaften beider zu vereinen. Bei Carbon bestehen diese zwei Werkstoffe aus den Kohlestoff-Fasern und dem entsprechenden Epoxidharz als „Klebstoff“. Diese Kombination wird zum einen extrem stabil und bleibt zum anderen unglaublich leicht.
Carbon bringt einige Vorteile mit sich. Es besitzt eine hohe Dauerfestigkeit, ist ultrastabil, steif, korrodiert nicht und bietet Gestaltungsfreiheit bei der Konstruktion. Carbon ist jedoch anisotrop. Demnach kann Carbon Belastungen hauptsächlich in Faserrichtung aufnehmen und weniger quer dazu. Dabei werden Zugkräfte in Faserrichtung wesentlich besser aufgenommen als Druckbelastungen. Daraus ergibt sich die Notwendigkeit die Fasern belastungsgerecht im Bauteil orientieren zu müssen. Erfahrungen bei der Auslegung, Konstruktion und Verarbeitung sind neben der Art und Qualität der verwendeten Materialen das A und O. Durch die Zusammenarbeit mit unseren auf Luft- und Raumfahrt spezialisierten Entwicklungsdienstleister Realize Engineering sowie diverser Forschungsvorhaben gemeinsam mit dem Institut für Leichtbau der TU Dresden und Unternehmen aus der Luftfahrt verfügen wir über Expertenwissen und kennen den aktuellen Stand der Technik, den sonst keiner in der Bike-Branche hat.
Carbon Fasern gibt es in einer ungeahnten Vielfalt. Es gibt verschiedene Gewebe, Gelege und viele Mischformen. Jede hat unterschiedliche Eigenschaften, die es heißt, richtig einzusetzen. In der Bike Branche hat man es hauptsächlich mit drei verschiedenen Carbon-Bindungen zu tun: der Köperbindung, der Leinwandbindung und dem UD-Gelege.

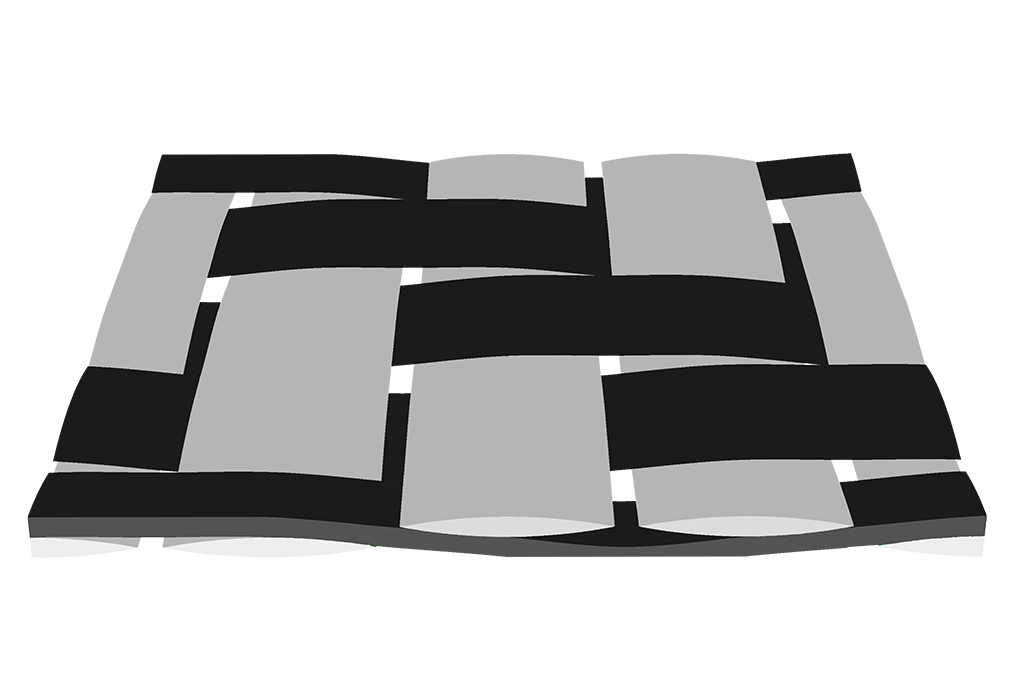
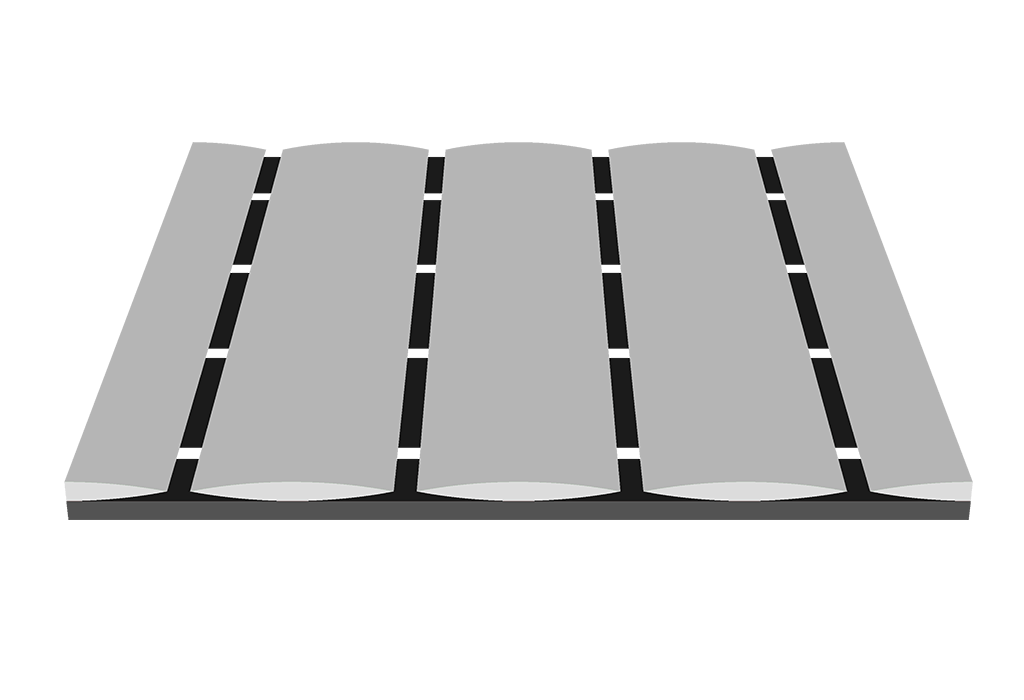
Die Leinwand- und Köperbindung sind Gewebe, bei denen die Carbonfasern nicht ideal gestreckt liegen, sondern regelmäßig, kurzwellige Krümmungen aufweisen. Je stärker die Ondulationen, sprich die Krümmungen sind, desto mehr werden die mechanischen Eigenschaften reduziert, da an den Fadenkreuzungspunkten komplexe Spannungszustände herrschen.
Bei der Leinwandbindung verläuft ein sogenannter Schussfaden abwechselnd über und unter einen Kettfaden. Bedingt durch die starke Faserkrümmung, weißt die Leinwandbindung unter den oben genannten Bindungsarten die schlechtesten Druck- und Ermüdungsfestigkeitswerte auf.
Bei der Köperbindung verläuft ein Schussfaden abwechseln über und unter zwei Kettfäden. Somit liegen die Carbonfasern gestreckter, als bei der Leinwandbindung. Die Köperbindung ist daher schiebefester und außerdem einfacher zu drapieren.
Maximale Steifigkeit und Festigkeit sind jedoch nur mit straff gestreckten Fasern erzielbar. Hierbei können UD-Gelege ihre Stärken ausspielen. Die Besonderheit der UD-Gelege besteht darin, dass die einzelnen Fasern nur in einer Richtung, unidirektional, ausgerichtet sind. Die Carbonfasern liegen also gestreckt, was wiederrum zu deutlich höheren Steifigkeits- und Festigkeitskennwerten führt. Es ist jedoch wesentlich komplizierter zu verarbeiten und benötigt viel Sorgfalt beim Auslegen.
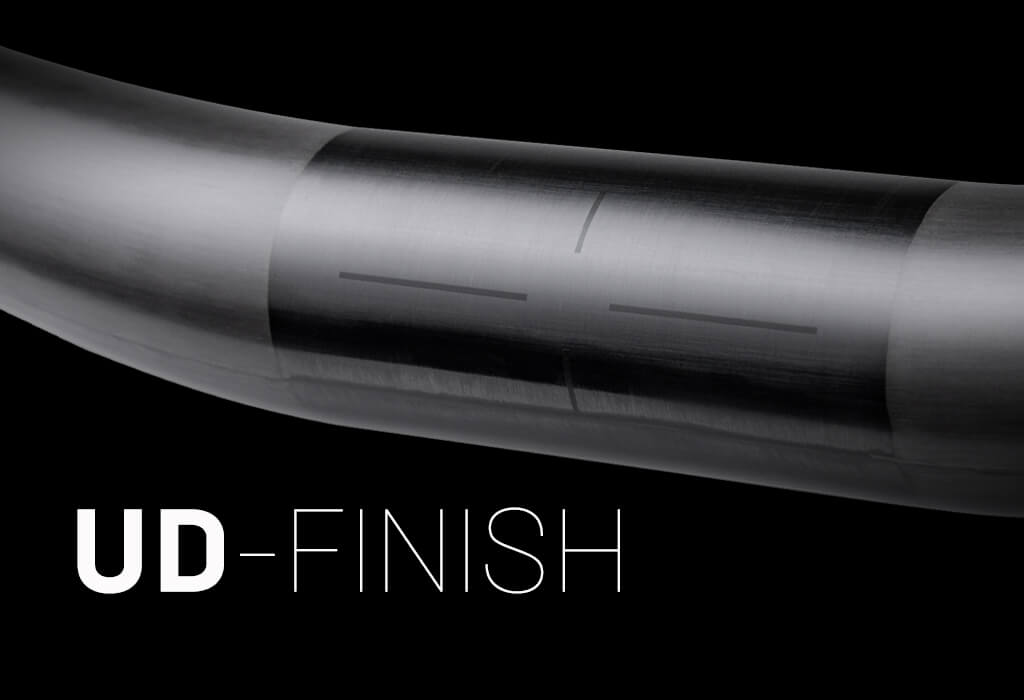
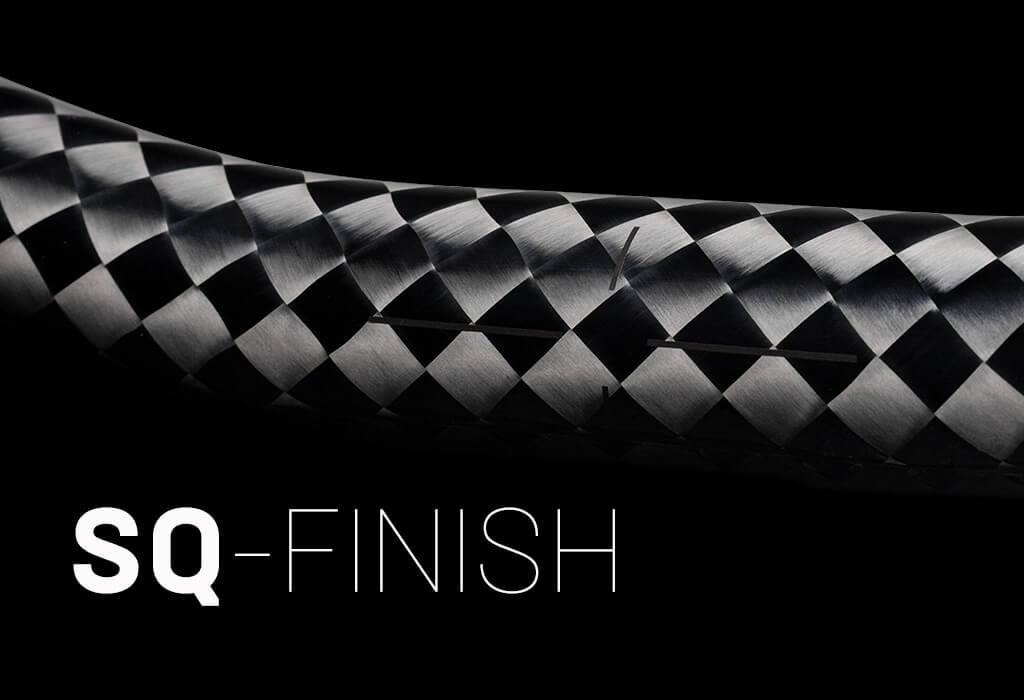
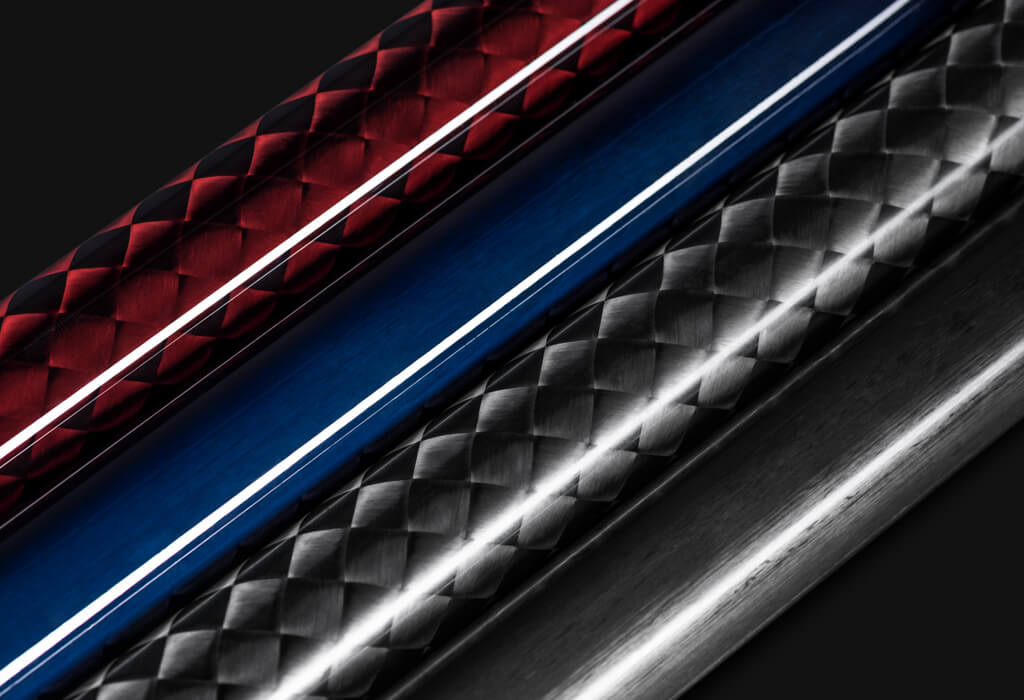
Wir bei Beast Components haben uns entschieden unsere Komponenten in zwei verschiedenen Optiken zu produzieren: dem UD-Finish und dem SQ-Finish. Dabei benutzen wir wegen der hohen Steifigkeit nahezu ausschließlich UD-Gelege. Beim SQ-Finish wird zusätzlich eine Sichtlage mit Leinwandbindung (Spread Tow) verwendet. Wir achten darauf, dass die Steifigkeit der Decklage an das darunterliegende UD-Laminat angepasst wird.
Den zeitlich höheren Aufwand in der Produktion durch die deutlich schwierigere Drapierbarkeit des UD-Gelege nehmen wir in Kauf. Für uns zählt in erster Linie, dass deutlich größere Festigkeitsniveau.
HIGHEND ENGINEERING
Auch bei uns beginnt alles auf einem weißen Blatt Papier. Zunächst werden erste Design-Überlegungen getroffen und unsere Ingenieure machen sich Gedanken über das Lastenheft, welches das jeweilige Bauteil erfüllen muss. Als Basis dafür werden die Ansprüche der härtesten Industrietests verwendet. Denn Carbon-Komponenten für Bikes müssen teils enorme Kräfte aushalten und dürfen dabei selbstverständlich nicht brechen. Mit Hilfe dieses Lastenheftes gehen unsere Konstrukteure ans Werk. Diese designen und entwickeln das Bauteil mit der CAD-Software CATIA. Davon abgeleitet entstehen auch gleich die Formwerkzeuge für unsere Komponenten.

Ein großes Highlight bei unserer Entwicklung ist die aufwändige Simulation mittels der FEM-Software ABAQUS jedes einzelnen Bauteiles. Dabei werden überwiegend nichtlineare Berechnungen mithilfe Bruch-Mode-bezogener Versagenskriterien (Cuntze-Kriterium) durchgeführt und mit nachgeschalteten Wöhlerlinien-Systemen ausgewertet. So können noch vor Produktionsbeginn bei den Bauteilen die Festigkeit und Verformungseigenschaften in einzelnen Belastungssituationen überprüft als auch eine definierte Lebensdauer vorhergesagt werden. Unsere Lenker beispielsweise werden zyklisch simuliert, während die Felgen in einer virtuellen Crash-Simulation untersucht werden. Dies erlaubt eine schnelle Entwicklung ohne unnötige Entwicklungsschleifen zu machen. Als Ergebnis dieser oft aufwendigen Simulationen erhalten wir präzise Layup-Pläne, welche auf die jeweiligen Belastungen hin optimiert sind. Anschließend werden Prototypen gebaut und auf unseren eigenen Prüfständen getestet, um die Simulationsergebnisse zu validieren.
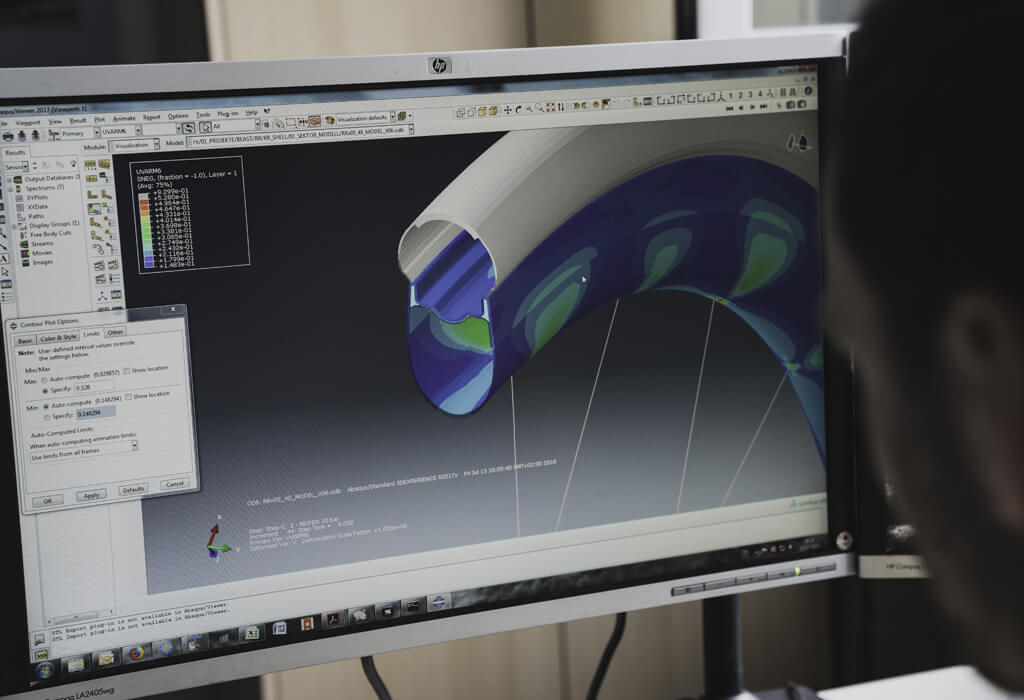
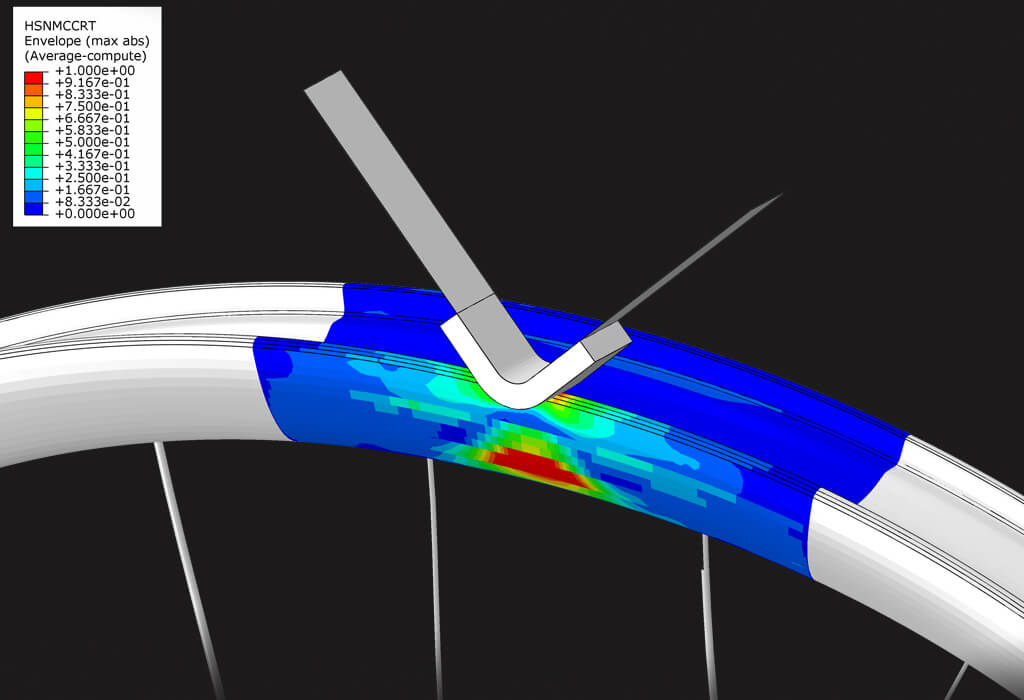
Durch diese wissenschaftliche Herangehensweise an die Konstruktion der Komponenten können wir bis an die Grenze des physikalisch Machbaren gehen, weil wir eben sehr genau wissen, wo diese Grenzen verlaufen. Dieses Vorgehen ist in der Bike-Branche ein absolutes Alleinstellungsmerkmal.
PRECISE PRODUCTION
Wir arbeiten mit dem Klassiker unter den Leichtbautechnologien für komplexe Bauteile – dem Prepreg-Autoklav-Verfahren. Dabei wird zunächst jede Lage der vorimprägnierten Faserhalbzeuge, den sogenannten Prepregs, maschinell auf die richtige Passform geschnitten.
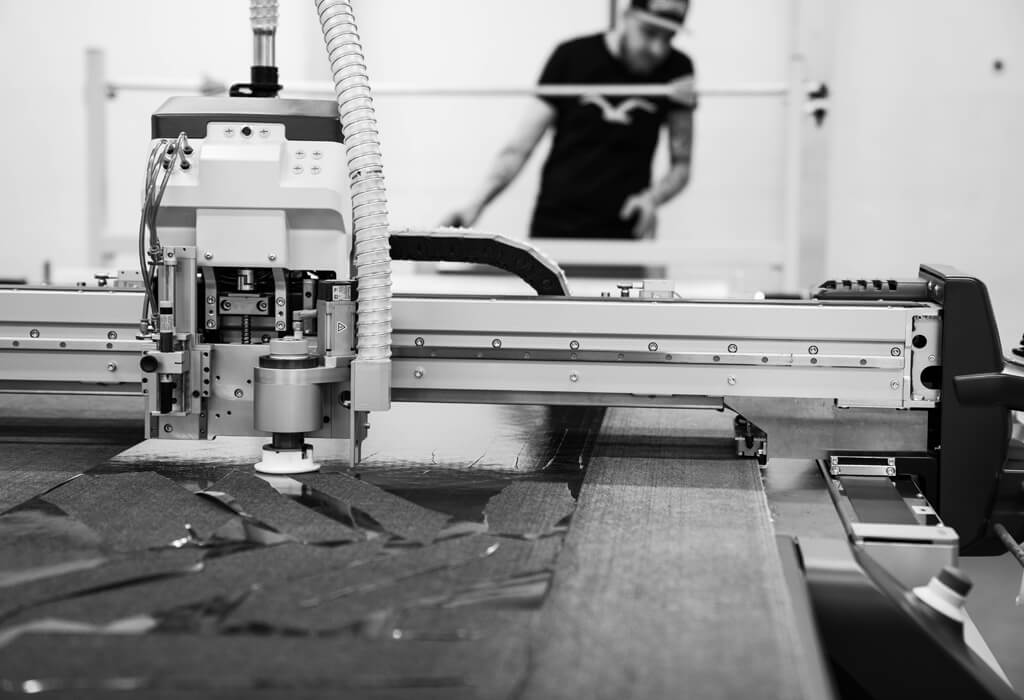
Anschließend geht es an das Laminieren, also das Auslegen der einzelnen Carbon-Lagen in die Werkzeugformen. Dies bedarf viel Geschickt, Genauigkeit und Erfahrung. So entsteht Schicht für Schicht jede einzelne Komponente. Wir verwenden sehr viele, dünne Carbon-Lagen, was ein höherer Aufwand der Produktion bedeutet, aber auch ein deutlich sichereres Bruchverhalten der Komponenten erzeugt. Um euch eine bessere Vorstellung von dem Prozess des Laminierens zu geben: Je nach Lenker müssen bis zu 84 Prepreg-Lagen per Hand nach einem bestimmten Plan verlegt werden.

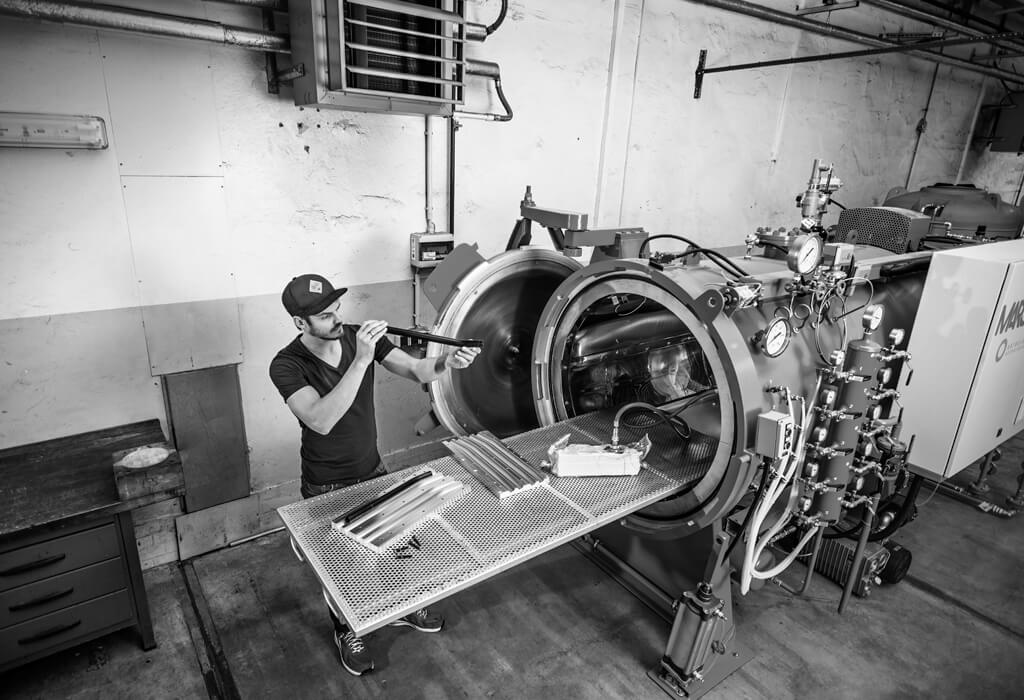
Nachdem die Techniker in Handarbeit und großer Sorgfalt die Prepregs in entsprechender Reihenfolge in das Werkzeug gelegt haben, wird alles vakuumdicht für die anschließende Aushärtung in unserem Autoklav verpackt. Unter Druck, konstantem Vakuum im Werkzeug und Temperaturen zwischen 110°C und 150°C härten die Bauteile aus. Auf diese Weise verhindern wir Lufteinschlüsse und Qualitätsschwankungen.
Die Teile werden entformt und penibel überprüft. Die Lenker werden auf Fehler oder Unebenheiten untersucht. Nur konstruktiv perfekte Komponenten kommen dann in die optische Qualitätskontrolle.
Bei der optischen Kontrolle werden Komponenten mit Fehlern wie Blasen, Beulen oder Falten aussortiert. Kleinste optische Mängel, die ein ungeschultes Auge nicht erkennen würde, werden ausgebessert, aufbereitet und gefinisht.