UNSER PRÜFLABOR
BEHIND THE SCENES
Dank unserer aufwendigen Simulationen mittels der Finite-Elemente-Methode beim Engineering, wissen wir bereits vor dem ersten Test welche Belastungen der erste Prototyp meistern sollte. Dieses Vorgehen ist in der Bike Branche einzigartig und bestimmt zielgerichtet die weiteren Entwicklungsschritte. Das sonst übliche Trial-and-Error Verfahren bleibt uns erspart.
Trotz alledem gilt: Möchte man an die Grenze des Machbaren gelangen, Komponenten möglichst leicht und dennoch enorm stabil herstellen, dann sind Prüfstände ein absolutes Muss. Unsere Tests dienen nicht nur der Entwicklung und Weiterentwicklung, sondern vor allem der fortlaufenden Qualitätskontrolle unserer Produkte und der Validierung unserer FEM-Simulationen.
Keine Simulation und kein Test ersetzten natürlich die Realität. Zahlreiche erfahrene Biker prüfen unsere Produkte auf Herz und Nieren und liefen uns direktes Feedback zu den Fahreigenschaften.
Wir testen weit über die gesetzlichen Mindestanforderungen hinaus. Eine besondere Herausforderung sehen wir im Enduro- und Downhill-Bereich, da hier teils enorme Kräfte auf die Komponenten einwirken. Aber egal in welchem Bereich ihr unterwegs seid, wir möchten, dass ihr unseren Komponenten zu 100% vertrauen könnt.
UNIVERSAL-PNEUMATIK PRÜFSTAND
Ein Teststand mit vielen Möglichkeiten. Egal ob Lenker, Vorbau, Sattelstütze oder Speichen – dieser Prüfstand ist ein Allrounder und bei uns täglich in Betrieb.
> LENKER UND VORBAU
Der Lenker wird zusammen mit dem Vorbau am Prüfstand befestigt. An beiden Enden des Lenkers werden im gleichen Abstand Hydraulikzylinder fixiert, welche für eine realitätsnahe Krafteinleitung sorgen. Die Zylinder können die Komponenten sowohl auf Druck als auch auf Zug belasten. Wie auch in der Realität ergeben sich daraus gegenphasige und gleichphasige Belastungen. So wird beim Sprung Druck aufgebaut und beim Wiegetritt am Lenker gezogen.
Genau wie die Tests der bekannten Prüf-Institute testen wir einen definierte Prüfzyklus mit unterschiedlichen Prüfblöcken, bestehend aus 6 Belastungssituationen:
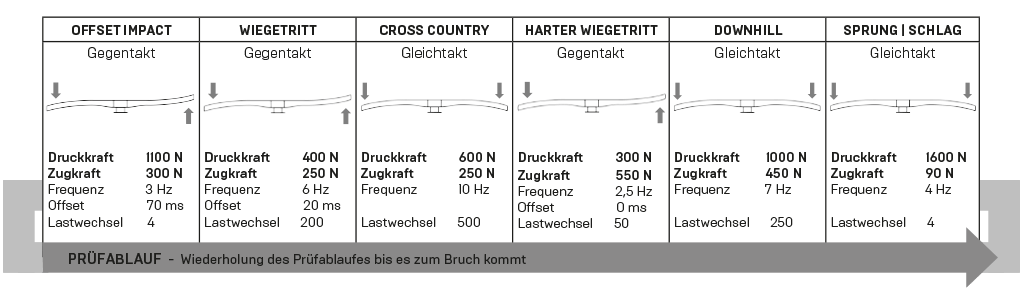
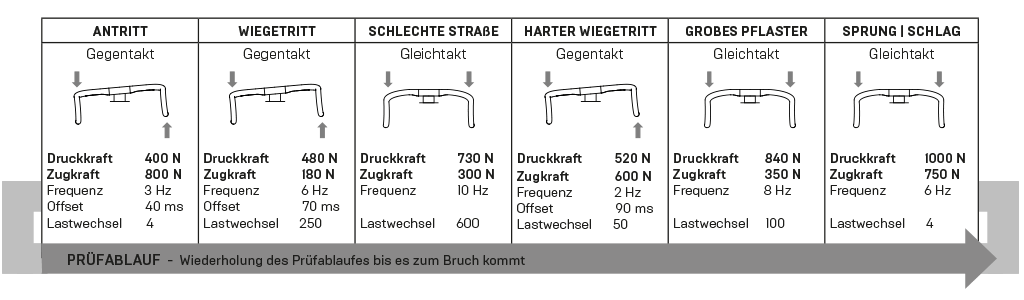
> SATTELSTÜTZE
Die Sattelstütze wird am Prüfstand mit einem Sitzwinkel von 73° befestigt. Die Krafteinleitung erfolgt 70mm hinter dem Mittelpunkt der Sattelklemmung. Zunächst muss die Sattelstütze den Normtest nach ISO 4210 bestehen. Im Anschluss erfolgt die Prüfung nach einem definierten Prüfzyklus. Dieser besteht aus drei weiteren Blöcken:
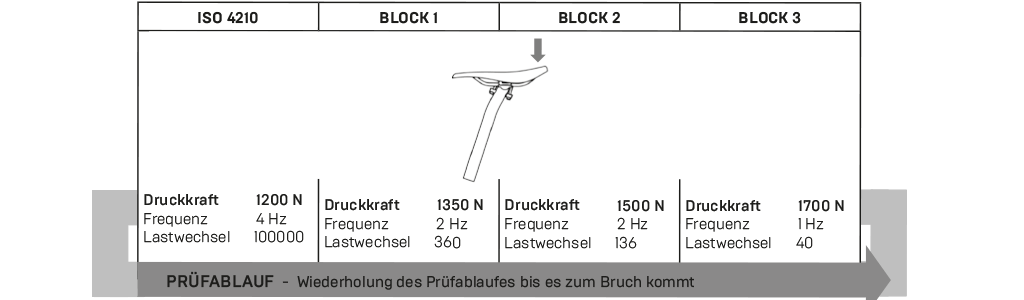
> SPEICHENAUSZUGS-TEST
Die Speichenlöcher sind besonders kritische Bereiche einer Felge und benötigen erhöhte Aufmerksamkeit. Mit dem Speichenauszugs-Test testen wir, welche Kraft eine Felge im Bereich des Speichenloches standhält. Dabei wenden wir einen statischen und einen dynamischen Test an. Beim statischen Test, wird an einer Speiche am immer gleichen Speichenloch 10-mal hintereinander bis zum Speichenbruch (bei ca. 3200 N) gezogen. Beim dynamischen Test werden 500 Lastwechsel bei 0,5 Hz mit einer Beanspruchung von bis zu 2000 N gefahren. Auch dabei kann es zu Speichenbrüchen kommen – die Felge darf jedoch keinerlei Beschädigungen aufweisen.
> STIFFNESS-TEST
Mit dem Stiffness-Test prüfen wir die Steifigkeit bzw. den Flex unserer Komponenten wie beispielsweise unserer Lenker oder Sattelstütze. Der Test lässt Rückschlüsse auf den Komfort unserer Komponenten zu.
IMPACT PRÜFSTAND
Mit dem Impact Test wird ein Durchschlag auf das Felgenhorn nachempfunden. In der Bike-Branche gibt es verschiedene Versuchsanordnungen. Um eine Vergleichbarkeit der Laufräder untereinander zu gewährleisten, ist es wichtig, dass bei jedem Versuch die gleichen Bedingungen herrschen. Wir haben uns für folgenden Versuchsaufbau entschieden, der unserer Meinung nach am realistischsten ist:
– komplett eingespeichte Felgen
– unter Verwendung des gleichen Reifens je nach Kategorie (z.B. Magic Mary beim MTB)
– gleicher Reifendruck von 1,6bar
– ohne Anstellwinkel
In dem Versuch fällt ein Amboss mit Gewichten auf einer definierten Höhe auf das Laufrad. Je höher die Fallposition, desto größer die Kraft. Das Laufrad wird an unterschiedlichen Stellen nach und nach mit kräftigeren Impacts konfrontiert, bis es zum Bruch kommt.
Bei der Entwicklung der Felgen ist uns wichtig, dass es beim Versagen nicht direkt zu einem Durchbruch kommt. Ein tolerantes und vor allem langsames Versagen nach einem Impact ist unerlässlich für die Sicherheit. Nach einem Bruch der Felge muss eine gute Reststeifigkeit gewährleistet sein, damit man sicher zum Stehen kommen kann. Wir gehen jedoch einen Schritt weiter und verlangen von unseren Laufrädern, dass ihr nach einem Bruch wenigstens noch nach Hause fahren könnt.
ROLLEN PRÜFSTAND
Der Rollenprüfstand ist ein Dauerbelastungstest, mit dem jedes unserer Laufräder auf im Fahrbetrieb auftretende Kräfte getestet wird. Je nach Laufradtyp wird der Test auf seine im Einsatzzweck herrschenden Bedingungen angepasst. So wirken auf die Laufrad-Typen unterschiedliche Gewichte, Geschwindigkeiten und Hindernisse. Die Hindernisse variieren dabei in ihrer Anzahl und Höhe und liefern somit realistische Belastungen, wie sie auch im Fahrbetrieb auftreten.
Nach 125.000 Umdrehungen hat das Laufrad insgesamt 750.000 Hindernisse überwunden. Sind Felgen und Speichen intakt geblieben, hat das Laufrad den Test bestanden.